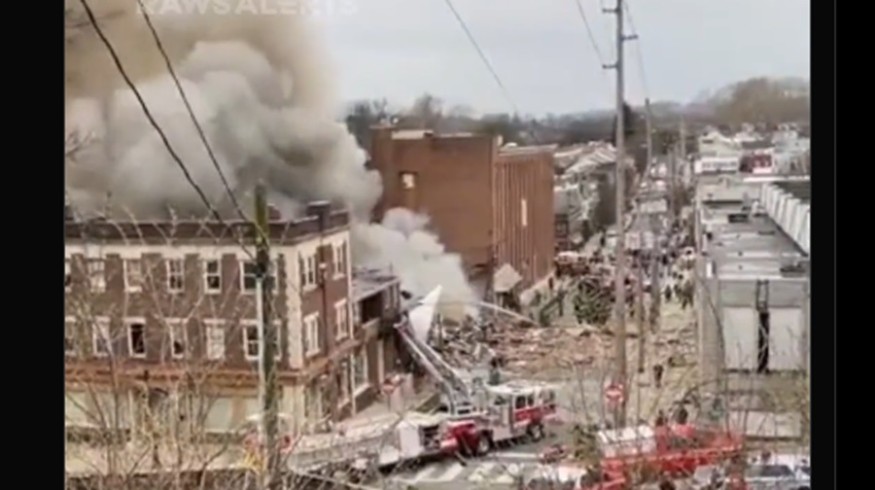
A deadly explosion at the RM Palmer chocolate factory in Pennsylvania in March 2023 was caused by a series of cascading failures involving a gas leak and inadequate safety protocols, according to the National Transportation Safety Board (NTSB).
Deadly Pennsylvania Chocolate Factory Explosion Linked to Gas Leak and Safety Failures
The blast claimed seven lives, injured several others, and caused $42 million in damages. Federal investigators revealed that a corroded steam pipe cracked, raising temperatures around a faulty natural gas fitting until it also failed, AP News said.
Gas then sped underground and ignited in the basement of one of the factory buildings. Workers had reported smelling gas before the explosion but were not evacuated due to a lack of proper emergency response procedures.
The NTSB criticized the factory's emergency protocols, stating they were insufficient to ensure worker safety. Employees were reportedly unsure whether the smell of gas required evacuation.
Chair Jennifer Homendy emphasized that confusion about evacuation policies likely contributed to the disaster's severity, noting that the company's current policy still leaves room for dangerous delays.
Approximately 105 people were inside the factory at the time of the explosion, split between production and office staff. Survivors have since accused the company of ignoring warning signs of a potential gas leak.
RM Palmer has expressed deep remorse for the tragedy and stated its commitment to improving safety measures.
However, the NTSB deemed the company's revised evacuation policies inadequate, underscoring the need for immediate and clear evacuation procedures when gas is detected.
UGI's Missed Warning on Corroded Pipe Cited in Factory Gas Explosion Tragedy
The investigation also highlighted the role of UGI Corporation, the utility company supplying gas to the factory.
According to PennLive, in 2021, a UGI crew replacing gas lines near the factory was alerted to the corroded steam pipe but failed to assess its potential impact on nearby gas infrastructure.
The safety board found this oversight, along with delays in shutting off gas after the explosion, contributed to the disaster.
A key component in the failure was a defective plastic service tee manufactured decades ago.
Known for its tendency to crack under heat, this type of pipe is still in use across the US, raising concerns about similar incidents in the future. The NTSB recommended identifying and replacing these aging pipes.
State and federal agencies are collaborating to implement stricter safety measures, including better pipe inventorying and gas leak alarms for buildings.
The Pennsylvania Public Utility Commission is incorporating the NTSB's findings into its ongoing investigation.
This tragedy serves as a sobering reminder of the importance of proactive safety measures in preventing loss of life and property. The final recommendations aim to ensure such an incident is not repeated.